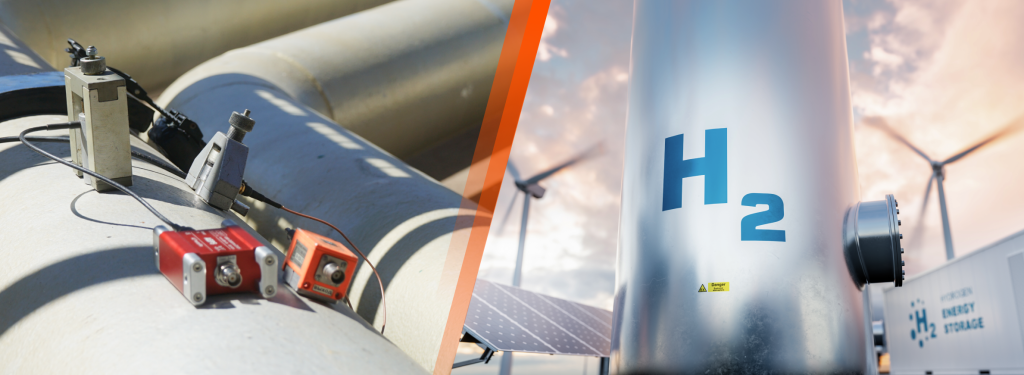
The importance of monitoring hydrogen plants
Nowadays, hydrogen plants play a crucial role in the production and storage of this gas. However, since these are considered ATEX atmospheres, they require strict precautions, especially in terms of the application of monitoring and predictive sensors, which allow these structures to remain within the standards.
To this end, we spoke with Bruno Moreira, Research and Development Engineer for advanced NDTs at EQS | a Kiwa company, who explained the importance of monitoring hydrogen plants and choosing the most suitable sensors.
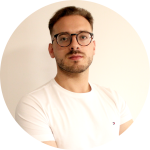
Bruno Moreira
Research and Development
Engineer for advanced NDTs
What are the main sensors used to monitor hydrogen plants?
At the moment, the most commonly used sensors in hydrogen plants are concentration and integrity sensors.
Concentration sensors are able to detect the presence and percentage of hydrogen in the air, using the PPM measurement (parts per million). Through this measurement, it is possible to identify possible leaks, for example in reservoirs or pipelines, which represent a huge risk for power plants, not only in terms of safety but also economically. There are sensors that continuously collect the air around them and, when they shine a beam of light on it, they can analyze it. If there are certain particles of a gas, this interaction will cause an increase in pressure in the chamber where the air is located. This variation allows the concentration and presence of the gas to be measured.
As for integrity sensors, monitoring is related to infrastructure degradation. Over time, structures deteriorate as hydrogen causes steel to corrode. Although it is slow, this corrosion process can generate small cracks in pipelines or hydrogen tanks, which are easily detected by sensors, making it possible to continuously assess the quality of the infrastructure.
I would say that these types of sensors are key to effectively managing risks in hydrogen plants.
What parameters should be considered when monitoring assets that store/transport hydrogen?
Just like the sensors, the most important parameters are concentration, which, as I mentioned earlier, helps us to easily detect leaks, and integrity. This last can be done, for example, using the Acoustic Emissions method.
Acoustic Emissions is one of the methods we run at EQS, in which we use acoustic sensors, previously placed in the pipelines. When a crack appears, energy is released, which propagates in the form of a wave throughout the structure. This acoustic wave is picked up by the sensor. Through some analysis, and depending on the type of signal we receive, we can figure out the problem we’re dealing with, which could be a crack, a leak, corrosion, or even, in some cases, total ruptures.
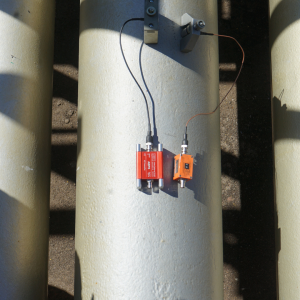
This method turns out to be the best to implement in hydrogen structures, as it allows us to analyze different data. For example, we can monitor the pipelines, since the acoustic sensors detect and send results about the state of the structure. It also allows us to understand where the problems are happening, through the wave that is picked up by the sensor. And sometimes we can even tell if the problem in question was just a single case or if there is a whole area of corrosion.
However, this method requires highly specialized professionals with very specific knowledge in this area, who are hard to find at the moment. Only these professionals can efficiently assess the condition of the structure and give good feedback to the client.
Is there any other type of sensor that should be mentioned?
There are also gas detection sensors that can indeed be used in hydrogen plants. This type of sensor detects the presence of gas in a given space by capturing it. If the sensor identifies the presence of gas, it immediately notifies you of the problem, so that you can stop production or transportation and take action to avoid disasters.
But in this case, you can only identify the problem after it has already happened, right?
Yes. These sensors only alert us to the problem after it has already happened, which means they are not monitoring sensors, nor are they part of the prevention of structures. They can detect the leak and allow us to act immediately. However, as they can’t predict the problem, they will always end up increasing the costs of, for example, maintaining and monitoring that area and its surroundings, and solving other problems related to stopping production and distribution, which come from a lack of planning.
Hence the importance of monitoring and the prevention phase in hydrogen plants. Early detection of leaks and other risks makes it easier to identify and stop problems, because it allows us to act with more time.
By using predictive sensors, we can notify our customers more quickly of possible risks and develop an action plan with them. This way, for example, we can take into account possible storage and transportation interruptions that may have to be made in order to carry out maintenance on the structures. In the end, prevention saves us money, resources and time, while maintaining production standards.
What are the prospects for future sensor developments in hydrogen plants?
Different solutions are currently being developed. One example is optical sensors, which work through functional fibers. Small segments of this fiber are distributed throughout the structure, usually coated with another type of material, such as palladium, which reacts to the presence of hydrogen by shrinking or expanding. By disturbing the shrinkage index, we can detect that something has gone wrong. Then, depending on the intensity of that signal and through the calibration curves, we can see the percentage of gas present. This gives us an idea of the integrity of the assets.
Basically, the material used in these sensors ends up being a mirror, in which only one wavelength is reflected. When there is any kind of change, a different wavelength is reflected and detected by the sensor (FBG – Fiber Bragg Grating). This indicator is used by our team to analyze the data, allowing us to prepare an action plan to be carried out.
For now, the sensors and methods I’ve mentioned are the easiest ways to monitor hydrogen plants, but this sector is evolving and it’s possible that in the future we’ll have new ways of carrying out this work.